超重力反应器
超重力反应器
超重力反应器湿式氧化法脱硫工艺中脱硫塔体积庞大、效率低、液体循环量大、运行 费用高等特点,将超重力旋转填料床作为吸收设备,形成了超重力湿式氧化法脱除硫化氢技术。硫化氢脱除率 95%以上,将硫化氢转化为硫磺,变废为宝,无二次污染。
- 所属分类: 超重力反应器
超重力法脱除气体中硫化氢
针对湿式氧化法脱硫工艺中脱硫塔体积庞大、效率低、液体循环量大、运行 费用高等特点,将超重力旋转填料床作为吸收设备,形成了超重力湿式氧化法脱除硫化氢技术。超重力湿法脱除硫化氢技术优势如下:(1)硫化氢脱除率 95%以上;
(2)脱硫气液比大于 100;
(3)气相压降小于 1000Pa;
(4)设备体积为传统塔的 1/10;
(5)投资与运行费用为塔式脱硫方法的 2/3;
(6)将硫化氢转化为硫磺,变废为宝,无二次污染。
本技术已成功应用于广西华银铝业发生炉煤气脱硫、天脊集团低温甲醇洗解 吸过程产生的含硫 CO₂尾气脱硫、山西太原东盛焦化厂、河北惠达陶瓷集团焦炉煤气脱硫和四川平武锰业氨法净化氧化锰行业中尾气硫化氢等工程项目,取得了良好效果。本技术可广泛应用于天然气、炼厂气、煤层气、合成气、焦炉煤气等各种含硫尾气硫化氢的脱除过程;可推广应用于天然气、变换气等加压脱硫系统,应用前景广阔。

中小型燃煤锅炉、窑炉排放的烟气相对大型电厂气量较小,一般在 3-30 万 m₃ /h,排放分散。采用电厂的湿法石灰石/石灰-石膏法烟气脱硫技术,不仅存在投资和运行费用高,设备易结垢、堵塞等问题,而且单级脱硫难以达到排放标准。
本技术可与双碱法、钙法、氧化镁法、海水法、碱法等多种脱硫工艺耦合,以提高传质效率,强化 SO₂吸收,单级脱硫率达99%以上。
该技术具有脱硫率和净化度高、液气比小、设备体积小、投资和运行费用低、适用范围宽等优点,已在山西运城、河南新乡等地建立示范工程,实现低成本、 ..率深度脱硫。超重力湿法脱硫技术可实现烟气脱硫除尘降温一体化,本技术适用于工业窑炉、转炉、化工企业及城市供热等中小型锅炉烟气的超低排放控制过程。

超重力法净化高浓度 NOx
火行业硝化过程中排放高浓度氮氧化物(俗称“硝烟”),污染严重、 治理难度大。传统常压净化技术釆用多级吸收但效果仍不理想,排放浓度高达 5000mg/m³左右。中北大学将超重力技术用于火行业高浓度硝烟净化治理,创建了超重力常压净化高浓度 NOx 的水冷工艺。釆用该工艺后,在进口浓度为 18000mg/m 的情况下,通过两级深度净化超重力吸收,结合还原分解塔工艺,硝烟浓度可降到 240mg/m³以下,NOx 排放量削减了95%,达到了排放标准。相比现有塔设备,成本可降低 30%以上,节省投资 75%,运行费用降低 79%,为有效解决高浓度硝烟污染问题提供了新方法,具有良好的工业化应用前景,已在山西兴安、甘肃银光等地建立示范工程。

超重力吹氨脱硝技术
针对 SCR 脱硝系统中液氨气化工艺存在的装置庞大、 隐患等问题,采用 “超重力氨水吹脱”替代“液氨气化”,消除危险源,实现本质 。将超重力化工过程强化技术应用于氨水吹脱,幵发适用于脱硝过程的超重力 吹氨设备及技术,吹脱氨水中游离的氨至气相,以此作为氮源加入到炉内脱硝, 大大提高了脱硝率,减少了污染,具有设备体积小、生产成本低、本质 性高等特点。
该技术应用于山西平朔煤砰石发电有限公司,单台设备处理氨水量为 0.1-0.8m³/h,稀释空气用量为 1000-2400m³/h,氨水吹脱率可达 95%以上,NOx 排放浓度小于 100mg/Nm³,氨逃逸浓度小于 8mg/Nm³。

超重力脱氨..技术
合成氨、碳酸铵、硝酸铵、硫酸铵、纯碱、硝酸磷肥等化工生产过程中产生的含 NH³类废气,气量大、浓度高,且含大量水汽和粉尘等杂质。在处理过程中,粉尘等杂质在水汽冷凝过程中会形成泥浆类物质,导致塔设备堵塞、NH³回收率低,难以稳定运行。通过创新超重力装置,研发了防堵型专用填料,实现了脱氨..一体化,脱氨率90%以上,达到氨和水的资源化利用。在天脊集团硝酸磷肥尾气治理技术改造工程实现工业应用,在39米平台狭小空间进行安装和实施,废气量55000m₃/h,氨含量8.3g/m ₃,水汽体积含量20.6%,含尘量3g/m₃ ,温度 70℃,以硝酸磷肥生产工艺中原有硝酸废水为吸收液,生成硝铵溶液进入生产工艺系统回用,实现..脱氨..,脱氨率92%,年回收氨 2940 吨,..率60.8%,年回收水3.86万吨,经济效益每年882万元。本技术推广应用于亚洲大的缓控释肥基地-山东金正大的脱氨..工程。

超重力法净化气体中 VOCs
含VOCs的废气是石化、火、精细化工、医药化工等生产过程中产生的常见化工废气,具有刺激性和强腐蚀性,治理难度大。基于VOCs的理化特性和相似相溶原理,开发超重力专用填料及装置,解决化工废气强腐蚀和动密封工程化难题,实现了..率吸收,净化率达到 90%以上,..了后序处理的负荷。本技术成功应用于某企业生产工艺中含醋酸废气的净化回收工程,以水为吸收剂,采用不锈钢多孔波纹板改性亲水性填料,气量4500m₃/h,当吸收液中醋酸浓度达到 70%时转入精馏工段,精馏后醋酸浓度达 99%以上,年回收醋酸 527 吨。该技术可推广应用于醋酸、丙酮、乙酸乙酯等混合溶剂的回收过程。

煤化工过程压缩机进口煤气除尘除焦油
现代煤化工生产过程中,煤制气净化后常需压缩机加压,煤气中少量的焦油、粉尘等杂质容易堵塞压缩机活门,影响正常生产。超重力除尘除焦油技术具有以下特点:
(1)实现高精度净化,焦油、尘浓度可降至5mg/m³以下;
(2)液体用量小,操作气液比高达2000左右;
(3)气相压降小,低于800Pa;
(4)可用造气循环水作为洗涤液,方便可靠。
本技术应用于贵州开磷息烽合成氨一期20万吨/年合成氨压缩机进口半水煤气除尘技术改造项目,进口含尘量60mg/m³左右的工况下,除尘率可达90%以上,净化后尘含量低于5mg/m³,..了压缩机长期稳定运行。
本技术可广泛应用于合成氨、焦炉煤气制甲醇、煤制氢等项目的压缩机进口气体的深度净化过程。

超重力煤锁气净化技术
“煤锁气"是煤加压气化过程中,由煤锁泄压而放出的含有尘和焦油的煤气,工况下为常压,需经压缩机加压后才能进入后续工序。新疆广汇新能源有限公司气柜出来的煤气中焦油尘含量超过1000mg/m³,造成压缩机堵塞,无法正常运行,煤锁气只能点天灯,造成了环境污染和资源浪费。超重力湿法除尘技术釆用造气循环水为净化介质,液体用量仅8m³/h,煤锁气中焦油尘含量约500-1000mg/m³左右。经超重力湿法净化后,煤气中焦油尘含量在 20-80mg/m³左右,净化率可达90%以上,年回收煤气 2.3亿m³。压缩机的工作周期从原来的 5 天提高到半年以上,净化效果良好。解决了煤锁气火炬燃烧排放造成的环境污染和资源浪费的行业难题。
本技术推广应用于新疆新天煤化工煤制天然气项目,具有良好的产业化应用前景。

化肥行业吹风气超重力除尘技术
随着雾霾天气的加剧,对于大气污染物的排放标准进行了多次调整。对于排放尾气中的尘含量提出了低于5mg/m³的超低排放标准或是20mg/m₃的特别排放限值。常用的布袋除尘、静电除尘、湿式电除尘技术对于低浓度含尘气体和超细颗粒物的净化都存在效率下降的问题。超重力除尘技术用水洗涤净化气体中的粉尘等细颗粒物,可实现超低排放,对于PM1.0仍然有 90%以上的净化效果,适用于串联在原有湿法除尘器后使用。本技术成功应用于河南心连心化肥有限公司的吹风气除尘,该公司经过回收的吹扫气经燃烧、换热、水膜除尘工序后,烟气含尘量为 100mg/m³左右,不能满足环保排放要求。建立了处量 80000m³/h的示范工程,超重力设备直径2200mm;釆用造气循环水作为净化介质,循环水量 26m³/h;出口尘含量低于12mg/m³;气相压降仅 800Pa,经济有效地实现了化工吹风气的超低排放。

超重力净化富铵钙尾气
本技术应用天脊集团的富铵钙尾气的净化与回收产品。在生产过程中釆用转鼓流化床造粒工艺,排出尾气中含有3000mg/m³的硝酸铵钙产品,气量为43000Nm₃/h,尾气的直接排放造成了部分产品的流失,同时也污染环境。但由于该尾气气量大,粉尘颗粒细小,常规方法除尘效果很差,除尘设备极易堵塞,不能长期正常运行;同时,富铵钙生产装置在22米高的平台上,空间位置十分有限(厂房内高度..5米),传统除尘设备因除尘效率与空间布置问题受到限制。采用本技术净化富铵钙尾气,超重力除尘装置直径1.6米 、高3.5米,安装于生产现场室内,满足了厂房内布置的需要。长期运行结果表明超重力除尘装置除尘效果良好,出口气体中含尘量仅为 5mg/m³,除尘效率达到了99%以上,满足了环保要求。循环水量仅为 12t/h,吸尘后的液体可进入生产工序,回收了产品。

超重力-电化学废水治理技术
针对废水中有机物和COD等指标不能达标排放、废水治理效能不高的技术难题,研发出超重力多级同心圆筒式电化学装置及超重力-电化学废水治理技术。该装置具有大的电极比表面积、高的传质和降解效率、易自动化控制管理等优点。该技术无需氧化试剂,可解决废水治理过程中有机物含量高、可生化性差、传质受限而导致的能耗增加、治理效率降低的技术难题。相比传统电化学废水治理技术,超重力-电化学废水治理技术优势:
(1)有机物去除率达到80%-;
(2)废水处理时间缩短30%以上;
(3)处理效率提高20%以上;
(4)过程能耗降低10%-20%;
(5)提高废水可生化性、无二次污染、技术清洁、环保。

旋转盘反应器光催化降解有机废水
半导体光催化技术具有反应条件温和、绿色..、无二次污染等优点,但由于悬浮催化剂的分离困难、强亲水性导致的催化剂与污染物传质受限以及光反应器光子传递效率低等问题,使得光催化技术难于工业化推广应用。技术特点与优势:
(1)将催化剂负载或磁改性,解决催化剂的分离问题;
(2)通过有机物改性提高催化剂亲油性,解决催化剂与污染物传质受限;
(3)物料以薄膜流形式存在,传质速率快,光利用率高、表面更新快,更新速率是环形反应器的2倍;单位体积的光照表面积大,提高了光子的传递效率; 液膜中溶氧量提升,催化效率高。
应用效果:
(1)紫外光降解含酚废水:1L初始浓度100mg/L含酚废水,循环 30min,废水降解率;循环120min,矿化率90%以上;
(2)与Pickering乳液结合降解高浓度硝基苯废水,降解率98%以上。

超重力氧化法处理火废水
火废水具有排放量大、污染物浓度高、成分复杂、色度高及难生物降解等特点,现有技术难以实现低成本、..率治理。釆用超重力氧化法处理火废水技术可达到排放标准,具有良好的工业应用前景。本技术得到自然科学基金(U1610106)和火青年科技研究基金(HZY06020301-11 )的支持。技术优势在于:
(1)创新超重力臭氧氧化与超声波强化氧化耦合机制,形成难降解废水处理的新技术;
(2)超重力技术强化气液传质,提高了臭氧利用率,降低处理成本;
(3)超声波技术产生羟基自由基・oh,强化了臭氧氧化能力,提..率;
(4)硝基化合物去除率≥96%, COD去除率≥93%,可生化系数达到 0.3以上,满足后续生化工艺要求。
本成果可广泛应用于火、化工等行业DNT、RDX、HMX 等有机废水的降解过程。

超重力强化铁碳微电解催化臭氧降解硝基苯废水
提高处理效率、降低处理成本、缩短处理时间是氧化法降解有机废水的关键因素。基于以,提出超重力强化微电解催化臭氧降解硝基苯类废水的思路。 以硝基苯为对象,釆用廉价铁碳形成原电池,阴极的活性[H]将苯环上的-N0₂还原为易降解的-NH₂,阳极 Fe 氧化为 Fe²+, Fe²+催化O³产生氧化能力更强的・0H,利用超重力提高液相湍动程度和气液接触面积,促进O₃溶解,解决O₃传质受限的关键问题,提高0₃利用率,提升降解效能,达到可生化要求,实现“以废治废”的目的。本项目得到自然科学基金的资助,获发明.. 6 件 ,在 Chemical EngineeringJournal 等重要学术期刊发表论文12篇。项目的完成,为深度处理难降解废水提供新思路,对拓展超重力技术领域、催生新技术发展具有重要的科学意义和应用价值。

超重力深度处理难降解有机废水
臭氧的氧化技术具有反应速率快、处理效率高、无二次污染等优点,但存在臭氧水溶性差、利用率低等缺点。基于此,利用超重力提高流体湍动程度和气液接触面积,促进O₃溶解,解决O₃传质受限的问题;通过耦合Fe²+、H₂O₂、超声波等技术,实现低成本、高 效能降解芳香族硝基类有机废水。该研究获山西省青年基金等资助。硏究表明:超重力技术可提高臭氧的利用率,硝基化合物去除率96%以上, 可生化系数达到0.3以上。申报发明..12件,在 Journal of Nanoparticle Research 等期刊发表学术论文 24 篇。

超重力卤水提溴技术
针对我国卤水资源溴含量偏低这一现状,结合生产计术成熟程度及成本等方面的原因,国内普遍釆用空气吹出酸液吸收法制溴。目前该工艺液氯消耗量大、电耗高,溴素得率偏低,这直接导致能源与资源的浪费。本技术创新在于:
(1)提出超重力卤水提溴方法,形成成套工艺技术;
(2)提高了溴离子的氧化率,使氯气利用率提高、减小了配氯率,降低了氯气消耗量;
(3)溴离子氧化率的提高减少了提溴后工序及晒盐工序中设备的腐蚀性;
(4)提高了提溴率,减小了空气用量,运行成本降低31%;
(5)设备体积仅为传统塔设备的1/28;
(6)获得发明..1件:ZL 200910073665.4。

超重力吹脱氨氮废水技术
氨氮废水来源于化肥、焦化、炼油等多个行业,氨氮污染引起水体富营养化,破坏生态平衡,危害极大。氨氮废水治理难度大,列入战略发展的技术需求。对于高浓度氨氮废水的治理常釆用空气吹脱+生化处理的方法,吹脱设备多为填料塔,气体用量大,吹脱效率低。本技术创新在于:
(1)基于多年研究,形成超重力法吹脱氨氮成套技术;
(2)气体用量是传统方法 1/4 左右,能耗降低 38%;
(3)单程吹脱率可达 85%以上,接近气液理论平衡状态;
(4)2001 年获得山西省科技进步二等奖;
(5)2002 年被科技部列为重点推广项目。

超重力制备纳米零价铁并同步处理含硝基苯废水
针对纳米零价铁在制备、干燥、储存中存在易团聚、易失活等问题,提出超重力制备纳米零价铁并同步处理含硝基苯废水的思路。将纳米零价铁的制备与纳米零价铁还原硝基苯的反应耦合,在纳米零价铁制备中同步实现含硝基苯废水的快速处理。硏究结果表明:处理过程中,投加的铁离子适宜初始浓度约为硝基苯废水中硝基苯浓度
的20-30倍,硼氢化钠还原剂溶液浓度范围为铁离子初始浓度的2.0-3.0倍,停留时间仅3秒钟,硝基苯去除率即可达到。
本方法变多步为一步,避免了传统方法纳米零价铁制备过程中的洗涤、分离、干燥、储存等繁杂操作,极大地简化了制备及使用步骤,为含硝基苯废水的处理提供了一条简便、快速的新途径。

超重力技术制备纳米氢氧化镁阻燃剂及其应用研究
针对传统搅拌釜式反应器在制备纳米氢氧化镁的过程中存在产物粒径分布不均、质量稳定性差和氢氧化镁浆料沉降分离难等问题,本技术从强化微观混合的角度出发,提出以撞击流-旋转填料床为反应器,在制备过程中引入表面活性剂进行在线改性,实现了纳米氢氧化镁的一步制备和改性,幵辟了连续制备纳米氢氧化镁的新工艺。技术创新在于:
(1)该技术所得氢氧化镁浆料的沉降性能明显提高,其沉降速度是正向沉淀法的4.7倍,是反向沉淀法的12.4倍,是双向沉淀法的2.1倍;
(2)该技术所制备的氢氧化镁为六方片状、粒径小、粒度分布均匀、分散性好、纯度高且晶形完整,热稳定性好,满足阻燃剂的要求;
(3)该技术结合超重力沉淀法制备纳米氢氧化镁和在线改性法的优势,一步合成了表面有机化的氢氧化镁;
(4)获得发明.. 2 件:ZL 201310338819.4、ZL 201210561949.X。

超重力过程强化技术制备磁性纳米材料
磁性纳米材料传统制备方法存在不易连续生产、制备效率低,且所制备的纳 米材料粒径分布不均匀、易团聚的问题,严重制约了磁性纳米材料的应用拓展。 撞击流-旋转填料床(IS -RPB)利用高速撞击射流在强大离心力作用下形成的巨大的剪切力使液体微观混合与传质过程得到极大强化,使得微观混合均匀特征时间 远小于纳米粒子的成核诱导期特征时间,反应体系过饱和度高且分布均匀,由此制备的磁性纳米粒子粒径小且分布均匀,已成功实现连续制备超顺磁性 MFe₂O4(M=Fe、 Mn、Co、Ni)纳米粒子、金属单质及合金磁性纳米粒子、天然高分子基磁性纳米粒子、介孔磁性纳米粒子。本研究申报发明..3件,在Journal of Alloys and Compounds 等 SCI 期刊发表学术论文 8 篇。该技术工艺简单、可连续生产,所制备的磁性纳米材料检测和去除重金属离子效果显著,可为重金属的..治理提供新思路,对拓展超重力 技术应用具有指导和借鉴意义。

微撞击流-超重力反应器的构建及其应用
基于混合过程的多尺度效应,针对撞击流与超重力耦合时存在的结构、混合 尺度、处理量不匹配等问题,根据受限式撞击流的特点,并结合超重力机(或旋转填料床)的优势,构建微撞击流/超重力(MIS -RPB)反应器。主要研究微撞击流在介观-微观尺度下的混合机理,幵展其结构优化与并行放大研究,实现微撞击流与旋转填料床的高度集成。硏究表明,MIS -RPB 的微观混合效果明显优于 IS- RPB(撞击流-旋转填料床)。Mn/Co 基氧化物的合成是储能材料的硏究热点,其性能易受微观混合与沉淀过程的影响。因此,釆用 MIS -RPB 反应器来代替常规反应器,通过考察超重力场对反应沉淀过程中晶体成核与生长的强化与调控机理,进一步提升材料的电化学性能,为储能材料的发展提供新的技术,终形成“反应器构建-结构优化-应用评估”的完整体系。研究表明,经微撞击流制备的 Mn/Co 氧化物循环稳定性明显提高(1000 次衰减 4%)。

超重力多相流模拟
超重力多相流模拟围绕超重力化工过程中的流体流动和反应特性,采用协同多种模拟方法的优势,对超重力反应器进行模拟和设计,实现工艺过程优化。在 Aspen 引入超重力特有的持液量和传质系数等关联式,预测了减压精馏和萃取精馏中的操作条件对理论塔板高度等的影响规律,为其进一步放大提供理论基础;神经网络模型(ANN)可以高精度和快速的模拟实验结果,预测了吸附过程中的大吸附量和除尘过程中的分级效率,相比传统的经验关联式适用范围更广,相关系数达 0.99 以上;CFD 掲示超重力内的流场特性,如错流旋转填料床内液体分布、液膜厚度变化、压降和停留时间分布等。

超重力多相流可视化研究
由于超重力旋转填料床结构复杂,致使其内部流体流动规律以及液滴破碎机制尚不清晰。基于粒子图像测速系统(Particle Image Velocimetry, PIV)技术, 对超重力旋转填料床、撞击流-旋转填料床、旋转盘反应器内部流体流动形态、 液滴粒径、液滴速度分布等流动特性进行研究,建立了完整、可行的可视化研究方法。采用 PIV 技术对撞击流-旋转填料床的流场液滴的分布、液滴破碎模式、速度分布以及湍动能分布等流场流体流动特性进行研究,结果表明撞击流-旋转填料床中的撞击面直径与撞击初速度呈线性关系,在撞击中心湍动能大,混合程度较高,而在边缘处湍动能较小且
呈现随机分布;撞击后不形成回流,具有平推流反应器的特性。通过撞击流-旋转填料床可视化研究,为 IS -RPB 的结构优化提供理论与指导。

超重力强化三次采油用聚丙烯酰胺溶解熟化技术
以聚合物驱为主的三次釆油技术已经普遍釆用,常规聚合物配置站采用“分散-溶解(熟化)-外输”的短流程配制工艺,制约配制能力的核心问题是熟化时间和熟化罐数量,熟化流程釆用平台高架熟化罐搅拌熟化工艺,溶解环节所需时间很长,造成整个配置站设备体积庞大,数量多,占地面积大,投资和能耗高,建设周期长。技术特点与优势:在超重力场中,聚合物悬浮液经过旋转填料的微细通道, 被旋转的填料高频挤岀,切割为液丝、液雾状,使聚合物大分子链段间的作用力 快速减小,溶剂小分子渗入大分子链段的扩散速度瞬时加速,提高了溶解速度, 缩短了溶解时间。
应用效果:(1)设备体积小,易于撬装和分散布局;(2)溶解时间短,由传统法的 2.5-3.0h缩短为10min;(3)设备数量少,投资省,建设周期短;(4)连续化生产,效率高,有利于
推广应用;(5)聚合物母液浓度均匀,质量稳定。

超重力技术制备甲醇柴油乳化燃料
釆用撞击流-旋转填料床作为乳化装置制备甲醇柴油乳化燃料,是超重力技术在甲醇柴油乳化燃料制备工艺中的一次尝试,是传统工艺与..的一次结合。本技术显著的特色在于:油水两相在撞击流-旋转填料床装置中高速剪切、强烈分散,制备的乳化柴油具有稳定时间长、乳化剂用量少、粒径分布均匀等特点,更重要的是制备乳化柴油为连续操作,实现了 “现做现用”。本研究创新 IS -RPB 制备甲醇柴油乳化技术,可根据实际稳定时间需求,添加少量乳化剂和助乳化剂,达到降低乳化成本的目的,幵辟了乳化柴油连续制备的新工艺,实现了..、连续化操作。可推广应用于乳化石蜡、乳化涂料、乳化硅油等领域中。本研究获自然科学基金资助,授权发明..5件,专著1部,在Renewable Energy 等期刊发表学术论文 28 篇,其中ESI高被引1篇。
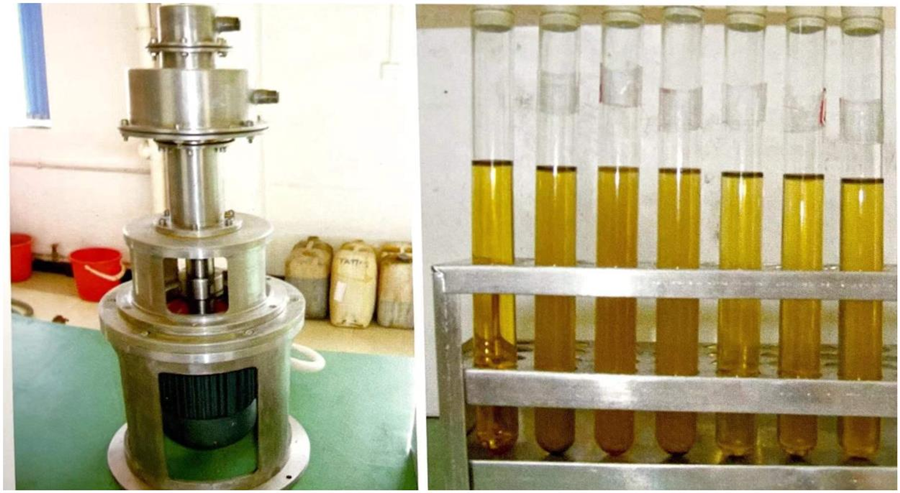
超重力精馏技术
传统精馏过程受重力场限制,气液相界面积小,表面更新速度慢,传质传热系数低,精馏设备体积庞大、能耗高。超重力精馏技术气液相界面积数量级增大,相界面更新速度快,大大提高传质传热系数,传质単元高度比传统精馏塔低 1-2 个数量级,气相压降为传统精馏塔 的 1/3-1/2,投资费用与能耗大大降低。
本技术形成了 4-6t/h 处理量的超重力精馏装备及工艺,可用于甲醇/水、乙醇/水、苯/甲苯等的分离,操作温度:0-150°C ,操作压力:一 0.095MPa-0.5MPa。。可单独使用,也可与现有塔联合使用。

超重力催陈白酒技术
新蒸馏出来的酒一般比较辛辣、暴冲、刺激性味大,需要经一定时间贮存, 才能使杂味消失。传统的白酒自然老熟存在陈酿时间长、酒体损耗大、占地面积大、资金积压严重等缺点。本技术创新在于:
♦创建催陈白酒的内循环式超重力装备与技术,获得发明.. (ZL200910075686.X);
♦实现了酒液在超重机内的自循环流动,避免了酒体损耗,..白酒基本品质;
♦白酒与含氧气体在旋转填料中进行微观尺度接触,强化白酒老熟过程中的分子缔合、氧化,有效控制挥发分小分子脱除;
专业品酒师评价:超重力处理新鲜白酒 1 小时,可达到陈放 1-2 年的自然老熟 效果,酒体醇和绵软。

超重力液-液萃取技术
在液-液萃取过程中,两个液相的密度差小,而粘度和界面张力较大,两相的混合与分离比气-液传质过程(如吸收、精馏等)困难得多,为达到理想的萃取效果就需要萃取设备有很好的混合与萃取传质性能。本技术研发了新型、快速、..的超重力萃取设备-撞击流-旋转填料床(is- RPB),利用其快速的混合特性,强化两相液体的混合传质过程,获得了 99%以 上的单级萃取效果。
本技术应用于含酚废水治理、稀醋酸溶液浓缩、铜矿浸出液提取等领域,萃取级效率高、相比范围宽、停留时间短、无溶剂滞留、适应性强、单位体积设备处理能力大、能耗低、易于工业化放大。
本技术 2006 年获得山西省高校科技进步一等奖。

上一篇:返回列表
下一篇:超重力法脱除气体中硫化氢